Konferenz-Bericht zum ECA Equipment Qualification Forum, 5./6. November 2024 in Heidelberg
Nachdem letztes Jahr die Version 2.2 des ECA Good Practice Guide "Qualification and Validation - A guide to effective qualification based on Customer - Supplier Partnership" veröffentlicht wurde, stand nun die neue Version 3.0 zur Veröffentlichung an. Diese wurde auf dem Equipment Qualification Forum im November erstmalig vorgestellt.
Autoren und Anwender des Guides erläuterten auf dem Forum gegenüber mehr 40 Teilnehmenden aus 13 unterschiedlichen Ländern dessen Inhalt, und Möglichkeiten der Anwendung. Zu Beginn der Veranstaltung gab der aktuelle Leiter der ECA Validierungsgruppe, Ralf Gengenbach, einen Überblick über den Guide und erwähnte die Veränderungen zur Version 2.2 aus dem letzten Jahr. Es wurden Inspektoren-Kommentare eingearbeitet und die Kapitel zu CARA (Critical Aspects Risk Assessment), der Kategorisierung und zu Remote Testings überarbeitet.
Ziel des Guides ist es, hinsichtlich einer "schlanken Qualifizierung" praktische Lösungen zu skizzieren, Fallstudien einzubinden und Musterbeispiele zu beschreiben. Der Guide verknüpft die Vorgaben aus dem Annex 15 zum EU GMP Leitfaden mit der FDA Process Validation Guidance und dem Ansatz der ASTM-Leitlinie 2500, s. Abbildung 1.
Abbildung 1: ECA Guide Focus - Supplier´s involvement
Basierend auf einem strengen risikobezogenen Prozess zeigt der ECA Guide die Einbindung von Lieferanten in den Qualifizierungsprozess. Er steht damit auch gut im Einklang zum ISPE Guide "Commissioning and Qualification" 2nd edition (2019). Die ISPE stellt den Prozessfluss in den Mittelpunkt, der ECA Guide fokussiert auf die unterschiedlichen Parteien und deren Aufgaben, die bei der Geräte-Qualifizierung mit eingebunden sind (Abbildung 2 auf Seite 28).
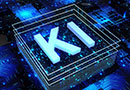
Seminarempfehlung
16. September 2025
Der Einsatz von Künstlicher Intelligenz bei der Qualifizierung und Validierung - Live Online Seminar
Abbildung 2: ECA vs ISPE Guide
Im Folgenden referierte mit Klaus Eichmüller, ein europäischer GMP-Inspektor, der aktiv an der Revision des Annex 15 mitgewirkt hatte. Klaus Eichmüller gab zunächst eine Übersicht über die regulatorische "Landschaft" bezüglich Qualifizierung und Validierung. Obwohl die Revision des Annex 15 mittlerweile 10 Jahre her ist, stellte er die Änderungen nochmals in den Vordergrund. Denn auch nach so langer Zeit sind noch nicht alle neuen Anforderungen in den Firmen umgesetzt. Er ging dann auf die Anforderungen an Lieferanten ein, die in die Qualifizierung eingebunden sind. Zwingend notwendig ist ein Vertrag zwischen Auftraggeber und -nehmer. Verantwortlich bleibt der Auftraggeber. Die Tätigkeiten des Auftragnehmers müssen vom Auftraggeber überwacht und geprüft werden. Er wies ferner darauf hin, dass auch eine Kategorisierung der Geräte möglich ist. Dieses Thema griff dann Maik Guttzeit an Tag 2 nochmals auf.
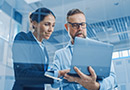
Seminarempfehlung
9./10. Oktober 2025
Schlanke Qualifizierung (QV 10) - Live Online Seminar
Abschließend zeigte er auf einer Folie Mängel bei Qualifizierungen aus seiner Sicht, s. Abbildung 3.
Abbildung 3: Qualification - problems
Wiederum Ralf Gengenbach griff dann das Thema Vergleich von Leitlinien auf. Als Punkte, die in Leitlinien unterschiedlich gesehen werden, nannte er u. a.
- Subject Matter Expert vs. QA (ASTM/ISPE vs. Annex 15)
- QCU vs Head of Production (FDA Process Validation Guidance vs EU GMP Guide I)
- Is the old V-Modell still valid, if yes, how to implement Risk Management?
Auch die Begriffe DQ, IQ, OQ, PQ werden in unterschiedlichen Leitlinien nicht immer gleich erwähnt oder fehlen gänzlich. Dennoch sieht er keine erheblichen Unterschiede bei diesen Qualifizierungsaktivitäten über die diversen Leitlinien hinweg. Die Überarbeitungen zum Kapitel Thema "Critical Aspects Risk Assessment" (CARA) stellte dann Rafael Leandro de Souza von Pharmaplan vor. Zu Beginn betonte Rafael de Souza, dass Geräte-Qualifizierung ein Lebenszyklus ist und sich dieser in Dokumenten wiederfinden müsse, um rückführbar zu sein. Anschließend zeigte er, wie ein CARA-Konzept in den Qualifizierungs-Lebenszyklus eingebettet werden kann, s. Abbildung 4.
Abbildung 4 "The CARA concept in the equipment qualification life cycle"
Die erste, als "QRA 0" bezeichnete Qualitätsrisikoanalyse, identifiziert produktbezogene Risiken (CQA), produkt- und gerätebezogene Risiken (CPP) sowie produkt- und prozessbezogene Umweltrisiken (CTQ). Diese Parameter fließen in das Design eines Gerätes ein. Die Qualitätsrisikoanalyse 1 (QRA1) bewertet die Parameter aus der QRA0 im Hinblick auf GMP-Anforderungen. Die Bewertungen fließen in die Benutzeranforderung (URS) ein, die entsprechend der 3 CARA-Schritte dann ebenfalls dreistufig sind. Die QRA2, die im Rahmen der Design Qualifizierung erfolgt, bewertet das Design während des Design Reviews. Im Rahmen der QRA3 werden Teststrategie und eine GMP-Tracebility-Matrix erstellt. Die QRA3 begleitet auch die Kommissionierungs- (GEP) und Qualifizierungsphase (GMP). Woraus wiederum auch eine Teststrategie im Bereich von GEP und eine GEP-Tracebility-Matrix erstellt werden. Abschließend zeigte er anhand des ICH Q9-Risikomanagementprozesses, wie sich dessen Prozesselemente in den Risikoanalysen CARA 0-3 abbilden lassen, Abbildung 5.
Abbildung 5 "CARA and QRM"
Intensiv diskutiert wurde ein Vortrag von Dr. Clemens Borkenstein, ZETA GmbH und Rolf Bauer, Syntegon Technology GmbH, zum Thema Remote Testing bei Factory/Site Acceptance Tests (FAT/SAT). Die beiden Referenten, Clemens Borkenstein leitet die Untergruppe Remote Testing der ECA Validierungsgruppe und Rolf Bauer ist Mitglied dieser Untergruppe, stellten heraus, dass der ECA Guide der erste Guide war, der das Remote-Thema bei der Geräte-Qualifizierung aufgreift. Sehr ausführlich stellten sie dann eine Checkliste vor, worauf man vor, während und nach einem Remote-Test achten sollte. Neu in das Kapitel aufgenommen wurde eine Passage zum Thema Remote and Hybrid Testing. Es sind Tests bei denen am Computer jemand die Tests verfolgt aber auch Personal vor Ort ist, das die Tests dann direkt mitbetreut. In Praxisbeispielen zeigten sie dann, auch mit Video-Animationen, wie bei ZETA und Syntegon Remote-Tests durchgeführt werden. Der Vortrag mündete dann in Vor- und Nachteile von Remote-Tests, s. Abbildungen 6 und 7
Abbildung 6: Pros (for Live stream FAT)
Abbildung 7: Cons (for Live stream FAT)
Mit einem gemeinsamen Abendessen endete der erste Konferenz-Tag.
Tag zwei begann mit einem Vortrag von Maik Guttzeit von der Bayer AG. Er leitet die Untergruppe zum Thema Priorisierung in der ECA Validation Group. An zwei Beispielen, einer Waage und einem Gefriertrockner zeigte er die Schwierigkeiten auf, die vermeintlich einfache Geräte bei einer Kategorisierung zeigen könnten. Sein erstes Fazit war: Es gibt keine einfachen und klaren Antworten auf eine Kategorisierung. Er stellte danach ein dreistufiges Kategorisierungsmodell vor, mit der Einteilung in:
- Non-critical
- Low-critical
- Critical
Und untermauerte diese Kategorien mit Beispiel hinsichtlich Qualifizierungsaktivitäten. Maik Guttzeit zeigte dann für Gerätschaften, die "von der Stange" ("commercial off the shelf", COTS) kommen Vereinfachungen bzgl. DQ und IQ. Abschließend zeigte er den aktuellen Stand des Annex 9 des ECA Good Practice Guides, das sich mit Kategorisierung beschäftigt. Verschiedene Ansätze einer Kategorisierung sind möglich, so Maik Guttzeit (s. Abbildung 8):
Abbildung 8: Categorisation - Matrix Approach
- Ein Matrix-Ansatz mit einem Ampelsystem (rot, gelb, grün)
- Ein Entscheidungsbaum-Ansatz
- Ein tabellarischer Ansatz
Sein Schluss-Fazit war: Kategorisierung kann helfen Qualifizierungs-Aufwand zu reduzieren - sollte aber niemals die Qualität reduzieren.
Das Thema "elektronische Dokumentation" im Rahmen von Qualifizierungsprojekten behandelten Igor Krasula von Valicare und Dr. Clemens Borkenstein, jeweils mit Praxisbeispielen. Als Vorteile einer elektronischen Dokumentation nannte Krasula u. a.
- Bessere Lesbarkeit von Berichten und einfachere Übersetzungsmöglichkeiten, sofern erforderlich
- Verbesserte Datenintegrität
- Einfacheres Teilen von Dokumenten (z. B. um Freigaben zu erhalten)
- Schnelleres Dokumentieren und konsistentere Begriffe (bei Nutzung von Standardbegriffen)
- Elektronische Freigaben (z. B. über elektronische Signaturen)
- Direkte Einbindung von Testdaten (von der Ausrüstung selbst, von Kameras, Bedienpanel-Ausdrucke etc.)
- Einfachere und günstigere Archivierung
Er ging dann auf einen "traditionellen Ansatz (Scannen von Papierdokumentation) und einen "fortgeschrittenen Ansatz" ein. Bei diesem "fortgeschrittenen Ansatz" werden Qualifizierungs-/Validierungs-Dokumente elektronisch erzeugt, die Tests dort eingetragen und das Ganze elektronisch freigegeben, s. Abbildung 9.
Abbildung 9: Advanced Approach
Ganz wichtig war ihm, dass elektronische Systeme die Datenintegritätsaspekte nach den ALCOA+ und ALCOA++-Prinzipien erfüllt. Er nannte hier das PIC/S PI 041 als hilfreiche Unterstützung. Wichtig bei der Projektierung eines elektronischen Systems sind die Schnittstellen zwischen Lieferant und Kunden, die Workflows und das System selbst. In seinem Fazit kam Igor Krasula zum Ergebnis, dass einige Firmen noch am Anfang zur Umsetzung eines elektronischen Systems stehen, andere schon eines eingeführt haben. Aber die Welt wird sich von "Tonnen von Papier" bei einer Qualifizierung hin zu elektronischer Dokumentation entwickeln, so Igor Krasula. Das Highlight war dann aber die anschließende Live-Präsentation solch eines Systems. Sehr eindrücklich wurde klar, dass durch entsprechende Programmierung auszufüllender Felder, Fehlerquellen durch Fehleintragungen verhindert werden können.
Im vorletzten Vortrag ging Pia Loris von Drees & Sommer auf das Projektmanagement bei Qualifizierungsprojekten ein. Die hauptsächlichen Herausforderungen bei Qualifizierungsprojekten identifizierte Frau Loris anhand von 6 Themen:
- Komplexität des Prozesses (u.a kann die Integration verschiedener Systeme und Prozesse komplex werden)
- Mangel an Ressourcen (z. B. ungeeignete Lieferanten und Personal mit zu wenig Erfahrung können ein Projekt verzögern)
- Regulatorische Compliance (Änderungen in Regelwerken zusammen mit dem Vorhalten von Audit-Bereitschaft können zu einer Herausforderung werden)
- Technologische Herausforderungen (Die Validierung komplexer Software-Systeme und die zuverlässige Funktion der Anlagen können ein Projekt verzögern)
- Risikomanagement (Das Risikomanagement ist eine entscheidende Stellgröße in der Qualifizierung, kann aber schwierig sein und viel Zeit kosten - auch weil Pufferzeiten fehlen)
- Datenintegrität (Der Umgang mit großen Datenmengen und die Sicherung der Integrität dieser Daten kann ebenfalls eine Herausforderung werden)
An einem Übersichtsbild zeigte sie dann die Komplexität von Good Engineering Practice Aktivitäten versus Qualifizierungsaktivitäten, s. Abb. 10.
Abbildung 10: Good Engineering Phases vs Qualification Phases
Abschließend berichtete dann Dominik Unglaub von gempex am Standort in der Schweiz über seine Erfahrungen in Audits und Behördeninspektionen bezüglich der Gerätequalifizierung. Er startete seinen Vortrag mit der rhetorischen Frage: Wie tief steigen Inspektorinnen und Inspektoren bei der Geräte-Qualifizierung ein? Er erläuterte das an zwei Fallbeispielen, einmal ging es um 2 Inspektoren-Tage, das andere Mal um 4 Inspektorentage. Der Fokus lag jeweils auf den Benutzeranforderungen und der Dokumentation. Er gab dann Beispiele von Inspektionsbefunden:
- Keine Standardarbeitsanweisungen zur Bedienung, Reinigung und Wartung vorhanden, obwohl schon PQ-Tests durchgeführt wurden.
- Keine verbindliche Zeitschienen vorhanden zur Abarbeitung von Mängeln bei Qualifizierungen
- Über den Validierungsmasterplan wurde nicht sichergestellt, dass alle Mängel im Rahmen von Qualifizierungen mit Einfluss auf die Qualifizierung untersucht werden
Sein Fazit war: Das Schlüsseldokument eine Geräte-Qualifizierung ist die Benutzeranforderung. Die Rückführbarkeit in der Dokumentation ist essentiell. Die Detailtiefe bei Inspektionen in Bezug auf die Gerätequalifizierung hat in den letzten Jahren stark zugenommen. Das wurde aus dem Auditorium bestätigt.
In einem Workshop wurde noch der Einsatz von Künstlicher Intelligenz (KI), hier am Beispiel ChatGPT, im Rahmen der Qualifizierung gezeigt. Das Zusammenfassen eines Unterkapitels aus dem Good Practice Guide zum Lieferanten-Kunden-Verhältnis erfolgte via ChatGPT mit Bravour. Auf den spontanen Zuruf aus dem Publikum wurde sogar ein Song mit dem wirklich passenden Titel "Keep it confidential" erzeugt. Eine weitere KI generierte im Nachgang dann noch Musik dazu. Auf derWebseite der Validation Group www.validation-group.org ist der Song anhörbar.
Aber wo Licht ist, ist auch Schatten. Bei einer ppm-Berechnung versagte ChatGPT völlig. Fazit auch hier: Der Einsatz von KI bei der Geräte-Qualifizierung kann wirklich hilfreich sein, z. B. bei der Erzeugung von Berichten. Allerdings sollte das Ergebnis immer kritisch hinterfragt werden.
Ein abschließendes Fazit zur Veranstaltung insgesamt: Die Vorstellung der Version 3.0 des ECA Good Practice Guide "Qualification and Validation, zeigten die Vorteile einer Präsenzveranstaltung. Das Social Event in der Heidelberger Altstadt gab Möglichkeiten zum Austausch, die so im Rahmen einer online-Veranstaltung nicht möglich sind.
Ein Verbesserungswunsch war, den Guide auch in einer einfachen Ausgabe, für (noch) weniger erfahrene Lieferanten im GMP-Umfeld zugänglich zu machen. Daran wird die ECA Validierungs-Gruppe in diesem Jahr arbeiten.
Der Guide ist für Mitglieder der Validierungsgruppe kostenlos erhältlich, s. www.validation-group.org
Über den Autor:
Sven Pommeranz
... ist seit 1996 bei CONCEPT HEIDELBERG und dort als Fachbereichsleiter für die Themenbereiche Validierung/Qualifizierung und Medizinprodukte verantwortlich.