GDP trifft CAPA - Umgang mit Abweichungen in Lager und Transport
Die Leitlinien der Guten Vertriebspraxis (GDP) und Guten Herstellungspraxis (GMP) fordern von Unternehmen die Implementierung effektiver Systeme für Korrektur- und Vorbeugungsmaßnahmen ("Corrective and Preventive Action" = CAPA).
Um sicherzustellen, dass CAPA richtig umgesetzt und genutzt werden, müssen zunächst alle Schritte identifiziert werden, die zu einem Ereignis, Risiko, Fehler oder einer Abweichung führen konnten - es muss also das "Problem" identifiziert werden, für welches eine Lösung erforderlich ist. Dann sollte man sich darüber im Klaren sein, dass die abgeleitete Lösung dauerhaft sein muss und keine negativen Nachwirkungen auf andere Geschäftsbereiche haben darf. Einfach gesagt darf die Lösung keine Probleme an anderer Stelle im System oder dem Unternehmen verursachen, weder unmittelbar noch in Zukunft.
Bevor in einem Unternehmen Korrekturmaßnamen und Vorbeugungsmaßnahmen ermittelt werden, ist es wichtig, mittels eines systematischen Untersuchungsprozesses jedes Glied in der Ereigniskette durchzuarbeiten, um tatsächliche oder mögliche Fehler oder Abweichungen von der erwarteten Norm zu finden. Und noch vor Beginn der Untersuchung müssen die in einem CAPA-System genutzten Definitionen richtig verstanden werden (siehe Zusammenfassung).
Ein ordentliches Abweichungsmanagement liefert eine Grundlage für den Entscheidungsprozess, basierend auf:
1 Nachweis: dokumentieren Sie alles, was bekannt ist, mit Verweis auf z.B. SOPs, Luftfrachtbriefe, Kopien der Versandpapiere, Temperaturausdrucke etc., falls vorhanden
2 Objektivität: Seien Sie off en, ehrlich, präzise, klar und akkurat.
Der erste Schritt ist, das Ereignis richtig zu erkennen. Was wurde gemeldet (siehe Tabelle 1 für Beispiele)?
+/- Abweichung im Lagerbestand | Falsche Rechnungsnummer angegeben |
Beschädigte Waren | Produktfreigabe vor der Genehmigung durch die sachkundige Person |
Falsches Produkt versendet | Fehlende Güter |
Temperaturabweichung | Ausfällung von Inhaltstoffen |
Dokumentationsfehler, z. B. falsche/fehlende/gefälschte Unterlagen | Falsche Füllmenge |
Tabelle 1: Beispiele für Ereignisse, die tatsächlich gemeldet werden
Diese Nachweise werden genutzt, um den weiteren Verlauf eines Ereignisses zu protokollieren oder eine Untersuchung für eine Abweichung aufgrund von z.B. Trendanalysen oder Kundenbeschwerden einzuleiten.
Im Abweichungsbericht werden die im Abweichungsmanagement gesammelten Nachweise festgehalten. Zu diesem Zeitpunkt sollte der Prüfer der Abweichungen zum Beispiel fragen:
- Welche Entscheidungen wurden getroffen?
- Wer hat die Entscheidungen getroffen?
- War die Person dazu befugt?
- Welche Information oder Nachweise wurden angebracht, um die Entscheidung zu begründen?
- Wie genau sind die schriftlichen Verfahren?
Weitere Fragen stellen sich:
- Sind die SOPs klar und akkurat, mit definierten Kompetenzen und Verantwortlichkeiten?
- Warum wurde das Personal nicht für bestimmte Verfahren geschult?
- Warum hat das Personal Verantwortungen übernommen, welche einem anderen Bereich zuzuordnen sind?
Der nächste Schritt ist, die "unmittelbare Korrekturmaßname" zu protokollieren. Auch wenn sich das einfach anhört, könnte eine unsaubere Dokumentation zu einem Wiederauftreten desselben Ereignisses führen.
Im folgenden Beispiel wurde ein Abweichungsbericht auf Grund einer unterbrochenen Kühlkette generiert. Das protokollierte Ereignis ist "wegen einer offenen Kühlschranktür hat die Kühlschranktemperatur +8°C für 10 min. überschritten". Die "unmittelbare Korrekturmaßnahme" ist, "die Kühlschranktür zu schließen". Es wird dokumentiert, was vorgefallen ist und ob Produkte betroffen waren. Um eine Wiederholung zu vermeiden, sollte das Personal daran erinnert werden, sicherzustellen, dass die Türen nach jedem Betreten/Verlassen ordentlich geschlossen sind. Dies beendet den Untersuchungsbericht: wenn die Temperaturüberschreitung keine Auswirkungen auf die Produktintegrität hatte, gibt es keine Untersuchung und "keine CAPA". Die verantwortliche Person sollte regelmäßige Kontrollen durchführen, alle Erkenntnisse fortlaufend dokumentieren, den Einfluss auf das Produkt (erneut) bewerten und ggf. die Betriebsabläufe prüfen.
Die Untersuchung bleibt jedoch off en, wenn sich das Ereignis wiederholt oder sich andere Erkenntnisse ergeben. Der Abweichungsprüfer sollte kontrollieren, wann der Kühlschrank zuletzt gewartet wurde. Gibt es zum Beispiel Probleme mit Türdichtungen, Scharnieren oder Kühlmittel? Eine Korrekturmaßnahme könnte sein, einen Techniker hinzuzuziehen. Und wieder stellen sich Fragen (siehe auch Methoden unten):
- Wurde das Problem gemeldet? Wann? Und an wen?
- Was ist passiert?
- Wer hat die Entscheidungen getroffen?
- Wessen Genehmigung wurde eingeholt?
- Wurde irgendetwas hiervon dokumentiert?
Jetzt geht die Untersuchung in Richtung der Identifizierung von Ursachen und der Durchführung einer Ursachenanalyse. Ordentlich durchgeführte Untersuchungen führen zur genauen Identifizierung der Ursache und damit zu angemessen Korrekturmaßnahmen sowie, wenn nötig, entsprechenden Vorbeugungsmaßnahmen. Man gelangt zu der Erkenntnis, dass CAPA(s) das Ergebnis von in Ursachenanalysen korrekt identifizierten Ursachen sind.
Abb. 2: Abweichungs-Management und die typischen Untersuchungsschritte zur Erreichung einer Grund-Ursache unter Berücksichtigung der Risiken des zu lösenden Problems und der Auswirkungen von Entscheidungen
In diesem Beispiel könnte es daran liegen, dass das Wartungs- und Instandhaltungsprogramm für den Kühlschrank aus Gründen der Kosteneffizienz ausgelaufen ist, dass bei Management-/Personalveränderungen das Instandhaltungsprogramm nicht berücksichtigt worden ist oder dass das Qualitätsmanagementsystem nicht ausreichend dokumentiert, welche Geräte in Gebrauch sind und welche Geräte regelmäßige Wartung und Instandhaltung erfordern. Aus solchen Erkenntnissen würden sich entsprechende Korrekturmaßnahmen ableiten (siehe Abbildung 2 für eine Zusammenfassung). Um CAPAs angemessen zu identifizieren und durchzuführen, muss die Abweichung richtig gehandhabt werden. Dies erfordert die volle Unterstützung des Teams und der Unternehmensleitung.
In den meisten Unternehmen obliegt der Qualitätsabteilung die Hauptverantwortung für Abweichungen und CAPAs. Der Prüfer hat die oberste Verantwortung dafür, vollständige Untersuchungen durchzuführen und ein Team zusammenzustellen.
Diese Abteilung sollte den Prozess überwachen und bewerten, über seine Effektivität Meldung machen und die Prüfer wenn nötig beim Prozess unterstützen. Die Abteilung sollte das Unternehmen mit den Werkzeugen, die es benötigt, ausstatten. Sie sollte jedoch nicht in die mit individuellen Abweichungen und CAPAs zusammenhängende Arbeit eingebunden sein.
Es gibt viele Werkzeuge zur Identifizierung von Ursachen und der Durchführung von Ursachenanalysen. Einige davon sind nachfolgend beschrieben.
Abb. 3: Dieses Fischgräten-Diagramm zeigt die Bereiche, die bei der Untersuchung zu berücksichtigen sind
1. Fischgrätenmethode (Ishikawa)
Die Fischgrätenmethode wird verwendet, um Informationen in Kategorien und Unterkategorien einzuteilen und damit zu ermitteln, welche Informationen verfügbar sind und ob diese mit dem Ereignis in Zusammenhang stehen. Für jede Kategorie werden so lange Auslöser identifiziert und ausgeschlossen, bis die Ursache ermittelt ist. Die "5 Warums" lassen sich mit dieser Methode gut kombinieren.
Abb. 4: Temperaturabweichung beim temperaturüberwachten Versand: Dieses Fischgräten-Diagramm betrachtet jeden Bereich genauer im Detail
2. Fehlermöglichkeits- und Einflussanalyse ("Failure Modes and Effects Analysis" = FMEA)
FMEA ist ein Werkzeug zur Risikobewertung, welches darauf ausgelegt ist, potentielle Fehler innerhalb eines Prozesses, Systems oder Designs zu finden und zu bewerten. Dazu werden alle bekannten Schritte in Bezug auf Schweregrad, Auftreten und Entdeckung systematisch geprüft und bewertet und anschließend alle Risiken nach Priorität sortiert. Eine Fehlermöglichkeit zeigt, wo potentiell Fehler auftreten können. Die Einflussanalyse prüft und bewertet den Einfluss dieses Fehlers und dessen Konsequenzen.
Deviation Handling
3. Die fünf Warums
Man fragt so lange nach dem "Warum?", bis die Ursache ermittelt ist. Die Anwendung dieser Methode zusammen mit anderen Werkzeugen ist im Abweichungsmanagement (Untersuchung) sehr hilfreich und ermöglicht es Prüfern, direkt von Experten zu lernen. Nachfolgende Fragen sollten dann auch mit "Wie?", "Was?" und "Wann?" beginnen, um Lösungen für das gemeldete Ereignis zu finden.
Um effektiv zu sein, erfordert diese Methode einen multidisziplinären Ansatz, um Erkenntnisse im Team zu erfassen und zu bearbeiten.
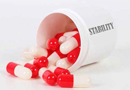
Seminarempfehlung
10/11 September 2025
Stability Studies to Support Shipping/Distribution of Pharmaceuticals and Biopharmaceuticals - Live Online Training
Zusammenfassung
CAPA
- Korrektur: bestehende Abweichungen beheben
- Korrekturmaßnahme: Ursache einer bestehenden Abweichung oder einer anderen unerwünschten Situation beheben, um deren Wiederauftreten zu vermeiden
- Vorbeugungsmaßnahme: Ursache einer potentiellen Abweichung oder einer anderen unerwünschten Situation beheben, um deren Wiederauftreten zu vermeiden
Grund-Ursache
- Soll den wahren Grund eines Ereignisses beschreiben Ursachenanalyse
- Prozess zur Identifizierung von Grund-Ursachen für ein Ereignis und zur Ermittlung eines Lösungsansatzes
- Soll Prozesse und/oder Systeme prüfen, um das (Wieder-)Auftreten von Ereignissen zu vermeiden
Autor:
Prabjeet Dulai
... ist Direktorin von GDP & Quality Matters Ltd. Mit Erfahrung im Management und als RP bietet sie der Industrie Beratungsdienstleistungen und Schulungen rund um GDP und verwandter GMP-Bereiche an.